Scaling Up Your Candle Making Business: Transitioning from Kitchen to Garage
Are you a passionate candle maker whose hobby has transformed into a thriving business? 🕯️✨
Congratulations on reaching this exciting milestone! 🎉
As demand for your beautifully crafted candles grows, you might find yourself faced with the challenge of scaling up your production operations. Moving from your kitchen to a dedicated workspace like your garage is a significant step towards meeting increased demand while maintaining quality and efficiency.
In this blog, we’ll explore the essential steps and considerations to help you smoothly transition your candle making business from the cozy confines of your kitchen to the more spacious environment of your garage.
And your family can enjoy having their space back while you move into a new space just for you! 🚀🏠
Assess Your Space
Before making the move, assess your garage space carefully. Consider factors such as:
- Size: Ensure your garage provides ample room for your equipment, supplies, and workspace. It should accommodate your current needs and allow for future expansion.
- Ventilation: Proper ventilation is crucial to maintain air quality and safety when working with candle-making materials. Evaluate the ventilation options in your garage and make any necessary improvements to ensure adequate airflow.
- Utilities: Check if your garage has access to electricity, water, and other utilities required for candle making. If not, you may need to install additional outlets or make other arrangements.
- Storage: Plan for storage solutions to keep your supplies organized and easily accessible. Shelving units, cabinets, and storage bins can help maximize space efficiency.
- Temperature Control: This is arguably your most important factor. Having standard temperatures for pouring ensures beautifully set candles. You may need windows for summer, and a warm room for winter, so double check if you need an A/C unit or can manage with opening and closing windows/doors.
Set Up Your Workspace
Creating an efficient workspace is essential for maximizing productivity and safety. Here are some tips for setting up your candle making area in the garage:
- Workstation: Designate a specific area for candle making activities, such as a sturdy workbench or table. Ensure it’s at a comfortable height and provides sufficient space for mixing, pouring, and packaging. You will probably may need 1+ table for setting, and one for mixing your raw materials.
- Safety Measures: Prioritise safety by installing fire extinguishers, smoke detectors, and first aid kits in your workspace. Familiarise yourself with proper safety protocols for handling hot wax and other materials.
- Organisation: Arrange your supplies and equipment in a logical layout to streamline your workflow. Use labelling systems to identify ingredients, tools, and finished products easily.
- Cleanup Station: Dedicate a space for cleaning up spills and messes promptly. Consider using washable mats or trays to protect the garage floor from wax drips and spills.
Invest in Equipment and Supplies
As you scale up your business, you may need to invest in additional equipment and supplies to meet demand efficiently. Some essential items to consider include:
- Melting Equipment: Invest in larger wax melters or double boilers to increase your melting capacity. Consider the type of wax you use and choose equipment that’s compatible with your preferred materials.
- Packaging Materials: Invest in quality packaging materials, such as jars, lids, labels, and boxes, to enhance the presentation of your candles. Custom packaging can help distinguish your brand and attract customers.
Streamline Your Processes
Efficient processes are essential for scaling up your candle making business. Focus on streamlining your production workflow to increase productivity and reduce waste. Consider implementing the following strategies:
- Batch Production: Adopt batch production techniques to produce candles in larger quantities while maintaining consistency in quality. Plan your production schedule to minimise downtime between batches.
- Standard Operating Procedures (SOPs): Develop SOPs for each step of the candle making process, including ingredient measurements, melting temperatures, pouring techniques, and curing times. SOPs help ensure consistency and efficiency in production.
- Inventory Management: Implement an inventory management system to track raw materials, finished products, and supplies. This helps prevent stockouts, minimise waste, and optimise reorder quantities.
Quality Control: Establish quality control measures to inspect candles for defects, such as air bubbles, uneven surfaces, or discoloration. Set quality standards and conduct regular inspections to maintain product integrity.
Transitioning your candle making business from the kitchen to the garage is an exciting opportunity to scale up your operations and reach new heights of success. 🚀
By carefully assessing your space, setting up an efficient workspace, investing in equipment and supplies, streamlining your processes, and ramping up your marketing efforts (stay tuned for another blog), you can effectively manage the expansion while maintaining the quality and integrity of your products.
With dedication, creativity, and strategic planning, your garage-based candle making venture has the potential to thrive and delight customers far and wide.
Happy candle making! 🕯️✨ Is this conversation helpful so far? 😊
Need more advice? Give us a shout: hello@illuminacandlesupplies.com
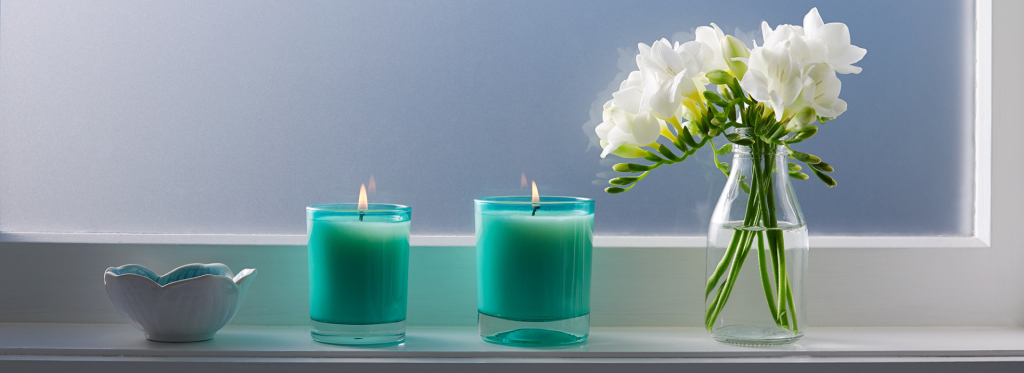